Medicines Manufacturing Innovation Centre: transforming the pharma industry
Find out how the Medicines Manufacturing Innovation Centre in Glasgow’s Advanced Manufacturing Innovation District (AMIDS) is leading the sustainable medicine revolution.

15 January 2023 | seven minute read
Established in 2018, The Medicines Manufacturing Innovation Centre (MMIC) is a collaboration between CPI, University of Strathclyde, UK Research & Innovation, Scottish Enterprise and founding industry partners AstraZeneca and GSK, dedicated to developing advanced solutions for pharmaceutical manufacturing.
The £88 million state-of-the-art facility brings world-leading science and technology expertise under one roof.
While the centre is on track to generate £200 million in technology innovation in the first five years, it’s set to have an even greater impact on the world of medicine manufacturing by making it more sustainable.
The global pharma industry generates greenhouse gas emissions of approximately 52 megatonnes of CO2 equivalent per year. This does not include any indirect energy-related emissions from the supply chain process, such as transportation or refrigeration.
“Pharmaceuticals, at their very core, exist to help people live healthier lives. But without a healthy planet, we cannot have healthy people”, writes Katie Murray, Technical Director at CPI, in her 2022 blog.
It’s clear that the global pharma industry must act to reduce emissions — and CPI has the solutions to support it.
A business model focused on sustainable practices
CPI’s aim is to redefine the future of pharmaceutical production with cutting-edge digital technology, collaborative expertise, and more sustainable manufacturing practices. To achieve this, the centre operates on a Grand Challenge model.
This model addresses the complex industrial hurdles that are currently limiting pharmaceutical manufacturing, such as resource constraints and high drug development costs. It currently has four key elements.
Switching to continuous manufacturing
CPI, and partners (The University of Strathclyde, AstraZeneca, GSK, Pfizer, Siemens, Applied Materials and Gericke) are developing a continuous direct compression (CDC) platform.
The hope is that this digitally twinned platform will transform oral solid dose formulation, development and manufacture. This will support the industry to shift to a more rapid response manufacturing approach that’s both cheaper and more energy efficient.
Transforming clinical trial supply chains
A key challenge of the pharmaceutical industry is long lead times, which can result in wasted medicine packs. The MMIC is delivering several digital clinical supply chain solutions that will increase speed, flexibility and efficiency in clinical trial drug manufacture. In doing so, it will reduce lead times, waste, and make it easier to respond to patient demand.
Driving digital manufacturing
Through the Digital Grand Challenge, CPI invites companies to join a Digital Membership which aims to unite pharma, technology, and delivery partners to standardise and speed up the adoption of connected technologies like AI and robotics.
This connected industry is widely known as pharma 4.0, and it will improve patient outcomes, increase sustainability and flexibility, and reduce costs.
Producing oligonucleotides sustainably
Oligonucleotides are short DNA or RNA molecules that have a wide range of therapeutic applications and the potential to revolutionise the approach to disease treatment, even finding therapies for currently ‘undruggable’ diseases.
CPI is developing revolutionary manufacturing processes for a more sustainable and large-scale production of them.
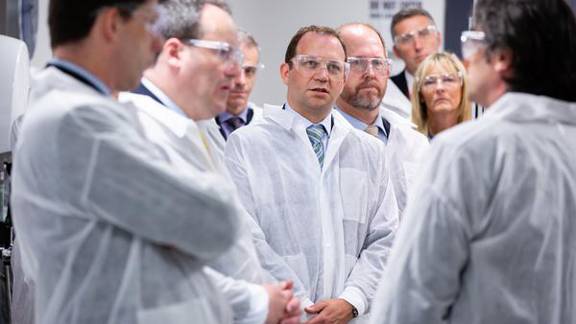
Minister for Business and Innovation Paul Wheelhouse is pictured with Scottish Government and MMIC colleagues.
Revolutionising the industry approach to medicines manufacturing
CPI is redesigning processes and developing solutions that will transform the industry’s approach to testing and manufacturing, making the process less harmful to the planet.
Digitising experiments
One of the key factors that will support the pharma industry to become more sustainable is the adoption of digital technologies, particularly in the testing phase of manufacturing.
Experiments that involve materials have a large carbon footprint, due to the materials and the processes involved in running the experiments. Virtual simulations of the same experiments allow scientists to run fewer tests, which vastly reduces the amount of material required.
CPI has developed a digital test-bed platform for the continuous direct compression (CDC) of tablets that combines a digital twin with a flexible, modular equipment platform.
The continuous nature of the CDC platform means there is no need for a granulation step, making the process shorter and less energy-consuming than the equivalent batch equipment that is currently used for making tablets.
If the pharmaceutical industry adopts this technology, the carbon footprint of process development and commercial manufacture will be greatly reduced.
Manufacturing medicines ‘just in time’
The pharmaceutical industry currently operates on a ‘just in case’ approach to clinical trial medicines manufacturing.
CPI aims to help push the industry towards a ‘just in time’ approach. It will do this through its Pharmacy Automation for Clinical Efficiency (PACE) platform. This will significantly reduce the lead time between a clinical trial site placing an order and receiving the patient's medicine packs.
Right now, the lead time is several weeks, which means orders are placed ‘just in case’. This often means that, by the time the orders arrive, the demand has changed considerably, which results in significant quantities of clinical trial medicine packs being wasted.
The PACE platform will enable orders to be placed much closer to real -time, reducing this waste and its associated carbon footprint by over 50%.
Developing new processes
CPI is currently developing a liquid-phase process that will considerably reduce the amount of solvent and starting materials used in the manufacturing and testing processes of oligonucleotide therapeutics.
Current manufacturing capacity for oligonucleotides is insufficient to keep pace with present and future demand, with lead times for clinical trial materials hindering the development of new therapeutics for patients.
CPI also has plans to develop an aqueous biocatalytic process soon, which would further improve the sustainability of oligonucleotide manufacture. This process involves enzymatic synthesis in a one-pot method.
This would move oligos into aqueous-based reaction media rather than using solvents like acetonitrile, which are harmful to the environment.
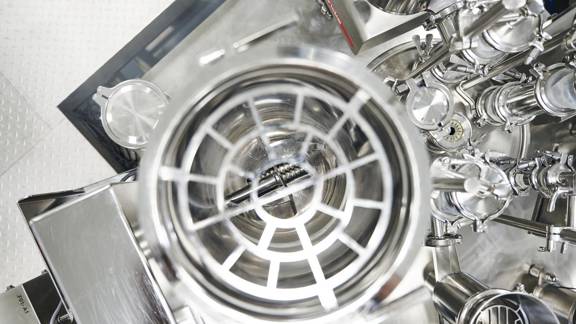
Supporting companies to overcome industry challenges
Not only is the MMIC helping to make the pharmaceutical industry more sustainable, but it’s also helping companies big and small to overcome some of the key challenges of the industry.
Technical and regulatory challenges are some of the main blockers for companies getting products to market. But CPI’s facilities, innovation and focus on knowledge exchange between industry, academia and government can help to overcome these and accelerate state-of-the-art solutions that will help people and the planet in the long term.
Looking to the future
John Arthur, Director of the MMIC said: “The impact of producing medicines on the environment is a huge challenge for the industry, particularly in the face of competing priorities.
"On the one hand, there is ongoing need for cost-effective medicines to fight cancer, dementia – there is still a long list — but we must pivot to new manufacturing processes and technologies which preserve and protect the environment.
“That’s one of the main challenges we are tackling at the MMIC and one which we look at holistically. Manufacturing medicines can be made more environmentally friendly in many ways and at a lower cost, whether we look towards digital solutions to accelerate the development of new drugs or innovative manufacturing techniques to increase efficiency and reduce waste.
"Our goal is to support the industry to make medicine available, affordable and sustainable”.
Got a question?
If you'd like to know more about MMIC or how we can support your business, just get in touch.
-
Sign up to exporting email updates
Stay updated with the latest exporting and ecommerce news, events and international market opportunities for your business.